Architectural Elements
This article appeared in Composite Technology, July/August 1996
By Susan Bassett, Infrastructure Editor
Architects Draft FRP for Decorative Elements
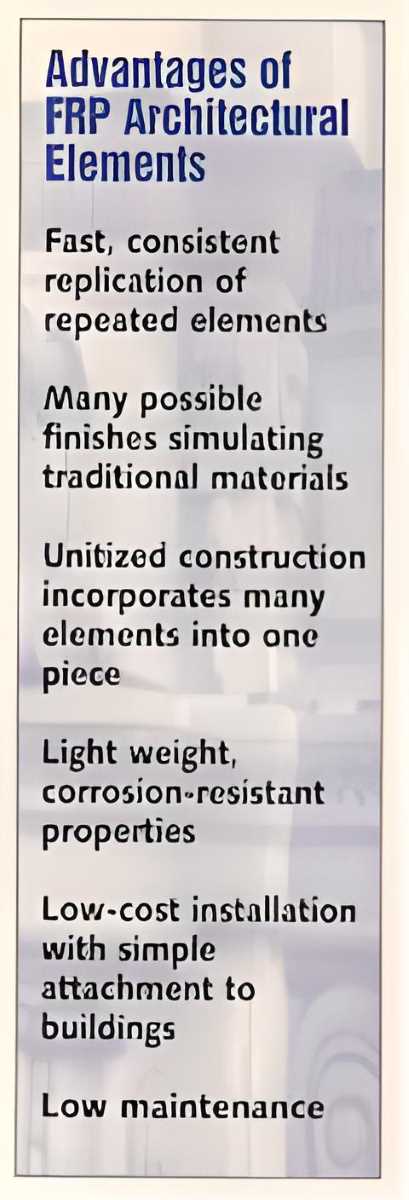
Offering ornate detail at significant cost savings, FRP ornamentation replaces traditional materials.
For specialty applications, fiberglass decorative architectural elements are fast becoming the first choice among building owners and architects. Not only is the installed cost of fiberglass less than that of traditional materials, but composites are easier to install and maintain.
Technological advances such as new finishes that better simulate traditional material make fiber-reinforced plastic (FRP) nearly indistinguishable from the real thing. In addition, heightened outreach efforts to the construction industry are convincing architects and contractors of the long-term benefits of FRP.
“It’s like trying to introduce a new tool to a carpenter. Like any other new material, it has to be presented in a waythat connects to what has been done in the past,” says William Kreysler, president of William Kreysler & Associates Inc. (Penngrove, Calif.), a composites manufacturer specializing in custom-built architectural elements.
Fiberglass decorative elements make it possible to achieve certain ornate styles. In many cases the cost would be prohibitive to use traditional materials, assuming one could find an artisan capable to do the work. FRP is ideally suited to decorative applications because intricate detail can be molded into thin fiberglass components. In fact, ornate details, such as steps, curves, brackets and lentils add rigidity to the material, says Charles Wittman, president of Architectural Fiberglass Corp. (Copiague, N.Y.)
Architectural elements encompass a wide range of decorative features including steeples, balconies, column covers, cupolas, dormers, friezes, pediments, railings, and window sills. Though frequently associated with old buildings, some of these distinctive elements are also incorporated into new structures, especially bank, university, library and government buildings. FRP is being used in the renovation of old buildings and in new construction.
FRP has already gained a majority share of the steeple market for several reasons. First, steeples are usually white, and white gel coats have historically weathered better than many colors. Second, their inaccessibility makes repainting extremely difficult and costly, making low-maintenance fiberglass a logical alternative.
Cost Savings Drive Acceptance
Complex fiberglass architectural elements boast lower installed cost and lower life-cycle costs compared to traditional decorative materials, such as painted wood, stamped steel, cast iron, copper, limestone, sandstone or terra cotta. However, these lower costs should not be interpreted to mean that the fiberglass elements themselves are cheap. Use of long-lasting materials and quality molding techniques produce a cost-effective product, but the most significant cost savings of these systems usually comes from reduced installation and maintenance costs.
At only 3/16- to 3/8-inch typical thickness, most fiberglass elements are substantially lighter than traditional materials. When these elements are installed high on a building, general purpose scaffolding and manual placement is sufficient. In contrast, traditional materials can require cranes and heavy scaffolding.
Another major cost savings comes from easier attachment methods. Typically, fiberglass elements can be screwed or bolted onto the existing structure without heavy steel supports or structural rehabilitation of the attachment areas on the building. Finally, labor cost savings can be achieved because general contract workers are frequently able to attach fiberglass elements.
“Fiberglass architectural elements can provide a ‘weight-loss’ system for buildings,” says Joe Czarnecki, national sales manager for Fibertech Corporation (Pendleton, S.C.). Large stone cornices and other outcroppings can become hazardous when the building’s supporting structure becomes too weakto carry the load of a solid, heavy material. But fiberglass elements, which typically weigh 1.5 to 2 lb. per square foot, can be attached to a building with less robust structure.
Cost savings also accrue over time from low maintenance. FRP does not rust, rot or erode. With highly weather- and UV-resistant gel coats, fiberglass surfaces need no paint. High-quality gel coat surfaces are expected to last at least 20 to 25 years (and possibly more) without significant deterioration. When deterioration does begin, the surface can be painted to extend the life of the elements. “Basically, you get the first several paint cycles for free,” Wittman says.
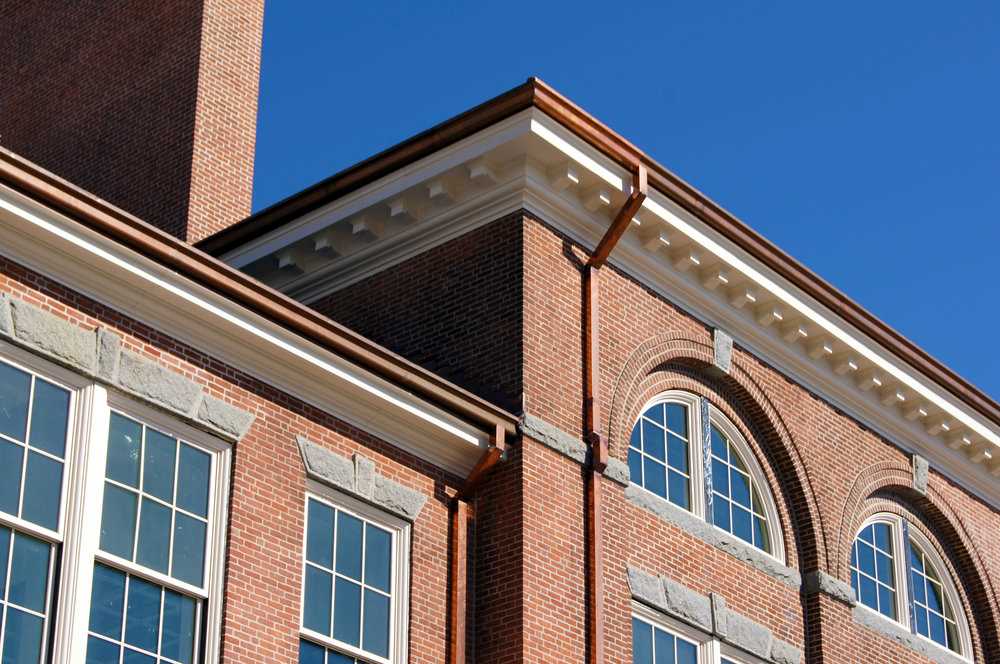
FRP on the White House
The balustrade on the rear façade of The White House has been restored using fiberglass components. Other landmark buildings now sporting fiberglass elements include the Plaza Hotel and the Equitable Building in New York City, the James Flood Building (see Figure) in San Francisco, St. Joseph Cathedral in San Jose and many others.
When faced with the replacement of deteriorating 70-year-old terra cotta cornices and window sills for the 40-story Equitable Building, owners feared that the New York City Landmarks Preservation Commission would require replacement with new terra cotta. However, Joe Micceri, restoration manager for the building’s owner, couldn’t find anyone qualified and able to produce the 62,000 square feet of terra cotta needing replacement. Architects for the project suggested fiberglass replacement and won approval from the preservation agency.
However, Micceri remained skeptical and required the work to be done in phases. After several years of work and $13 million, the deteriorated terra cotta was replaced with fiberglass elements produced by Rocca & Noto Inc. ( Long Island City, N.Y.), which has now adopted the name Architectural Molded Composites Inc. No longer skeptical, Micceri says, “I’m very satisfied with the material; it blends in so beautifully that nobody knows the difference if I do not point it out.” More than 10 years after installation, Micceri reports no problems with the fiberglass material and praises its
Outfitting New Buildings
Fiberglass are also being specified for new buildings. The Taj Mahal Casino ( Atlantic City, N.J.) and many other “theme” structures sport glitzy fiberglass decorative elements. In addition, new buildings replicating a period look are receiving fiberglass ornamentation.
A 10,000-square-foot Georgian-style residence in Jacksonville, Fla., is currently receiving fiberglass cornices. According to Mitchell McDaniel of Jacksonville-based McDaniel Contractors Inc., comparable wood or stucco cornices would cost at least twice as much as the fiberglass systems when material and installation costs are considered. McDaniel contacted several fiberglass manufacturers to find suitable stock molds for two different styles and sizes of cornices. The building has already received approximately 120 lineal feet of a cornice supplied by Architectural Fiberglass. Installation of this 4-ft-high by 2-ft-deep cornice was filmed for a recent broadcast of “Remodeler’s Showcase,” a television show available via cable and satellite. A smaller cornice produced by EDON Fiberglass ( Horsham, Pa.) has been scheduled for installation.
Residential uses are not for everyone, though. McDaniel estimates that ornamentation with these types of fiberglass cornices is restricted to residences costing $500,000 or more.
Design Considerations
When incorporating fiberglass architectural elements, several factors should be considered, not the least of which is aesthetics. To complement the architectural style of the building, the appropriate finish should be selected. Fiberglass can be molded into a number of different finishes to mimic wood, stone, terra cotta, concrete, steel or other materials. Additionally, in instances when people will interact directly with the elements, it is necessary to take into account the texture and solidity of the material. For example, polymer concrete works well as a substitute for many types of stone and concrete.
Manufacturers now provide a wide variety of stock elements. However, if an exact replica is needed, custom design and fabrication services are available. Loading (due to wind, snow, earthquake, pedestrians, and workers) and structural attachment of the fiberglass to the building must also be examined.
When decorative elements will be attached to an existing building, precise building measurements are crucial. Architectural Fiberglass Corp. prefers to have its own employees take measurements on site to ensure that any potential problems are identified before the elements are molded.
Fiberglass Specialties Inc. ( Henderson, Texas) integrated a number of different finishes when it produced a roof, cupola, and spire for the Stevens Institute of Technology in Hoboken, N.J. The project successfully replicated the look of slate shingles, copper and sandstone to match other parts of the existing building. After assembly on site, the entire roof, cupola and spire were lifted in one piece and placed atop the masonry tower. Three hours later, installation of the 18-ft wide, 45-ft tall structure was completed by bolting it to the existing masonry.
Element Design
Manufacturers have several design choices when creating decorative elements. In Fact, architects and contractors often request help from fiberglass manufacturers when writing the element specifications. For example, when specifying a cornice surrounding the top of a building, designers must consider how the
cornice joints coordinate with other linear elements on the building installation to determine the optimal number of sections. Cornice sections are usually 4 to 10 ft long and 12 to 60 inches tall.
The method of joining sections is also considered. When lap joints are used, one edge of a section overlaps the edge of an adjoining section. In contrast, when butt joints are used, the sections meet but so not overlap. Architectural Fiberglass Corp. prefers to build butt joints with full-depth walls (returns) at both ends of every cornice section. Once installed, the end returns of each roofed cornice section completely enclose a portion of the building. This design creates self-reinforcing modular rigid sections that often need no internal bracing. The full-depth returns (typically 6 to 42 inches deep ) also provide structural support to the roof of the cornice. Another advantage of this design is greater fire protection, since the use of flame-retardant resins in the end returns creates natural fire stops between cornice sections.
In contrast to butt joints with end returns, lap joints may be designed to fit sections together. On each cornice section, one edge steps down; the other edge is flat so that it will overlap the stepped edge on the adjacent cornice section. One advantage of these joints is that the sections can be cut in the field to the exact length needed. Because they use less material, the as-manufactured cost of this design is typically lower. However, the use of lap joints may increase installation costs, especially if internal bracing between the building and the fiberglass sections is required. Thermal expansion of different materials must also be considered when using internal bracing.
Manufacturing Process
Spray-up is the most commonly used manufacturing process for architectural elements. At Fibertech Corp. (Pendleton, S.C.), approximately 80 to 85 percent of the company’s architectural moldings use spray-up techniques, reports production manager Ray Longnecker.
Molds are commonly made of fiberglass and flexible rubber. Open fiberglass molds provide the most stability and can withstand higher volume use without distortion. Rubber molds are less dimensionally stable but provide more flexibility for making parts containing undercuts.
The most commonly used gel coat or exterior architectural applications is UV-inhibited NPG (neopentaglycol) isophthalic gel coat, which gives the best resistance to weather and UV light. The color of the gel coat can be customized to match the building, other decorative elements on the building or the caulk that will be used to seal joints between element sections.
Two types of resin are typically used for architectural elements. General purpose polyester resins are least expensive, but they are not formulated to retard fire. Class I flame-retardant polyester resins are formulate to meet the Class I standards, as defined in the ASTM E84 test method for measuring flame spread.
End-grain balsa wood is sometimes used in sandwich core FRP construction to produce additional stiffness. Wittman recommends sandwich core construction whenever a flat surface is more than 12 inches square.
If the finished part will be installed as a corner element, one of two manufacturing processes can be used. If only a few corners are needed, two straight pieces can be molded, miter cut and joined together. Architectural Fiberglass Corp. typically lays up fiberglass mat inside the corner to strengthen the joint. If quantities dictate, a corner mold can be built to produce a one-piece corner.
Installation
To facilitate installation, most manufacturers pre-fit pieces at their facility before shipping them to the site. Typically, adjoining sections are numbered and sent with a diagram showing the location of each piece. Careful shipment and handling of the bulky fiberglass shells is needed to prevent distortion or breakage.
Lightweight architectural elements are usually fastened to the building using screws or bolts. Masonry screws or bolts can attach the fiberglass elements directly to the building. More frequently, screws fasten the fiberglass to treated wooden blocks that are preinstalled on the building. To resist corrosion, all fasteners should be stainless steel, galvanized or coated with a corrosion-resistant material. In special cases where the decorative element does not include its own “roof,” special internal bracing may be built to attach the element to the building.
Since many elements are built in modular sections, a critical consideration when installing adjoining sections is to allow sufficient gaps between sections for thermal expansion. The coefficient of thermal expansion (CTE) for fiberglass is approximately 1.1×10 -5 inch/inch/ oF, which means that the fiberglass will expand and contract approximately twice as much as stone or steel. To prevent problems associated with varying CTE. Wittman suggests using a gap of 3/8-inch when sections are up to 12 feet long.
Once the fiberglass has been attached to the building, flashing is installed. Gaps between the building and the fiberglass elements are sealed with elastomeric polyurethane or silicone caulk. Gaps between element sections are also sealed.
Polymer Concrete Adds Needed Weight
Another composite material used in architectural elements is polymer concrete, a formulation of thermoset resins and aggregate that simulates stone. In some applications, particularly those within reach of pedestrians, a heavy material may be desirable to provide both the look and feel of stone or concrete. Kreysler and Associates advises that high-density core fiberglass with polymer concrete surface finish be used when the installed material will be within 10 feet of the ground. This heavy material is designed to simulate the solidity of stone so that there is no hollow sound if a passerby happens to tap it. The archway (see Figure) illustrates use of this high-density material to simulate sandstone blocks.
The company manufactures the simulated sandstone by first spraying a mixture of gel coat and sand to create the visible outer layer. Because the mixture contains approximately 40 percent sand, it is “barely sprayable,” says Kreysler, so the company has modified its spray equipment to handle the heavy mixture.
The high-density core is then manufactured by sandwiching a one-inch layer of polymer concrete between two layers of fiberglass. After being removed from the mold, the panels weight 10 to 15 lb. per square foot. A stone-like surface is created by sand-blasting approximately 10 to 15 mils of the resin from the exterior surface.
The exposed polymer concrete surface is even less susceptible to UV degradation than high-quality UV-resistant gel coat, since a high proportion of the surface is sand. The polymer concrete surface also has several advantages over real stone because it does not absorb moisture, dirt or graffiti.
Stone-like polymer concrete surfaces can also be created on lightweight fiberglass panels. The manufacturing process for these panels is similar to that described above, except that the 1-inch layer of core polymer concrete is replaced with a lightweight core or eliminated altogether. Lightweight matching elements are installed at heights more than 10 ft above ground level. Thus, FRP provides seamless visual integration of both heavy and lightweight materials, providing optimal properties based on their placement on a building.
Rapidly Expanding Market
Fibertech Corp. reports a 50-percent increase in demand over the past three years. “Architects are starting to come around,” Longnecker says. Kreysler estimates the current market size for composite architectural components at $30 to $50 million annually and growing at a healthy pace. “I would not hesitate to say that the market is likely to grow at the rate of 20 percent a year,” Kreysler says.
Sales of some types of architectural elements will outstrip others. According to Ben Bradshaw, sales and marketing manager of Fiberglass Specialties, the steeple market is already mature, due to fast FRP acceptance. Fiberglass Specialties sells about 500 to 800 steeples each year. In contrast, cornices and other fascia elements should grow significantly due to increasing requirements to inspect and upgrade old buildings. New York City requires fascia inspections of older buildings every five years and Chicago is expected to adopt a similar requirement. Deterioration discovered during these inspections should prove to be a market driver for manufacturers of FRP replacement elements.
Deborah Sack of the New York City Landmarks Preservation Commission, states that the agency “prefers to see architectural replacement with original materials.” However, the agency recognizes that many traditional materials (especially stone, terra cotta and wood) can be too costly. Synthetic replacement materials are approved on a case-by-case basis and the agency has approved many projects using fiberglass or fiber-reinforced concrete. Last year, a terra cotta cornice was replaced with a new fiberglass cornice on the Armani Exchange Building in the Soho Cast Iron Historic District in Manhattan.
Industry Actions Can Speed Acceptance
Fiberglass element manufacturers can take several actions to gain a larger share of the architectural elements market. First, the industry can continue work to educate building owners and the construction trades about the material. Manufacturers also often need to continue to work with owners, architects and contractors to ensure that all aspects of the project have been integrated. Wittman believes that clear specifications outlining the responsibilities of all parties involved in a project provide a good starting point. The publication and dissemination of the Composite Fabricators Association’s ( McLean, Va.) “Guidelines and Recommended Practices for Fiberglass Reinforced Plastic Architectural Products” is a positive step. The book includes a guideline specification to help architects and engineers draft clear, complete industry standard specifications for FRP decorative material.
Kreysler recommends that the industry can speed fiberglass acceptance by providing better documentation of past successes and clear, long-term expectations. While some fiberglass elements have been installed on buildings for more than 30 years, no compilation of these projects is available. Architects and contractors are looking for materials with proven track record but typically get only anecdotal evidence concerning fiberglass elements. Convincing documentation would allow fiberglass manufacturers to spend less time proving the capabilities of the material and more time discussing the project at hand.
Finally, some composite manufacturers are communicating in terms that the construction industry commonly uses. Since architects and builders are familiar with cast stone, Kreysler and Associates often describes its high-density core, FRP as “Synthetic cast stone.” Furthermore, the company specifies traditional attachments techniques for its products because architects, engineers and installers are already familiar with these methods.